What are Cavity Barrier Inspections?
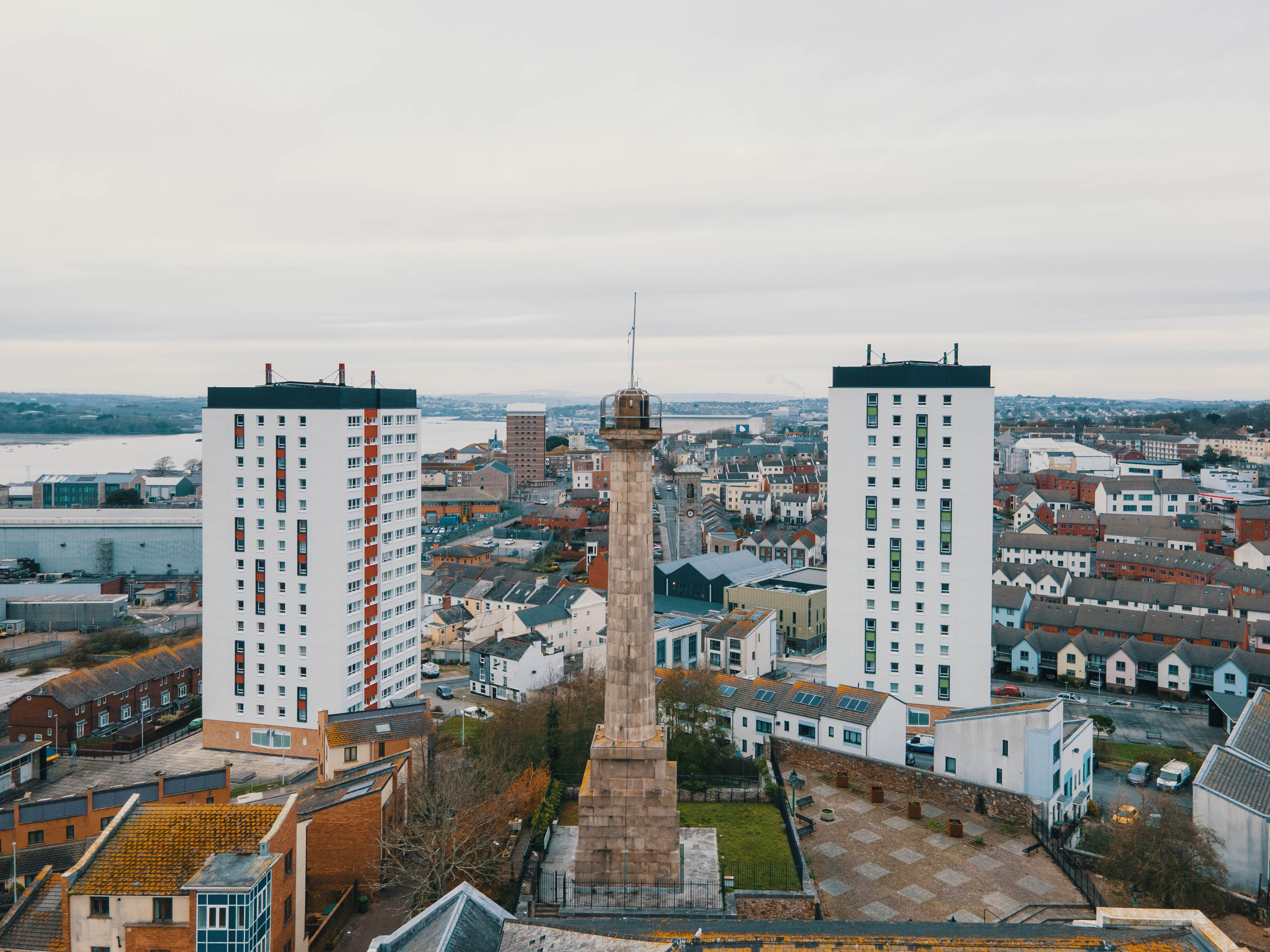
In todays blog, we delve into the significance of cavity barriers, the UK regulations governing them, the importance of regular inspections and answer some of the most frequent questions we get asked about cavity barrier Inspections.
What are Cavity Barriers?
Cavity barriers are crucial components of passive fire protection systems designed to prevent the spread of fire and smoke within a building. Installed within concealed spaces such as wall cavities, floor voids, and roof voids, these barriers help maintain compartmentation, limiting the rapid spread of fire from one area to another.
Cavity barriers come in various forms, including intumescent strips, fire-resistant boards, and expanding foam seals, tailored to specific building configurations and fire safety requirements.
Regulations and Standards
In the UK, compliance with stringent regulations and British standards is paramount to ensure effective fire safety measures, including cavity barriers. The Building Regulations, particularly Approved Document B, outline the legal requirements for fire safety in buildings. Additionally, British Standards such as BS 9999 and BS 476 provide guidelines for the installation, maintenance, and inspection of cavity barriers to uphold fire safety standards.
The latest revision to Cavity Barriers within Approved Document B of the building regulations highlights cavity barriers' utilisation in both new builds and renovation projects. The amendment mandates that all new structures adhere to cavity barrier standards of the utmost fire resistance during their design and construction phases. Moreover, existing buildings undergoing renovation or remodelling are obligated to incorporate cavity barriers retroactively if not previously installed.
Cavity Barrier Inspection Procedures
Conducting regular cavity barrier inspections is essential to verify compliance with regulations and ensure optimal performance in the event of a fire. These inspections involve a thorough assessment of cavity barriers installed throughout the building. Surveyors inspect the integrity, condition, and functionality of cavity barriers, checking for any signs of damage, degradation, or obstruction that may compromise their effectiveness.
Frequently Asked Questions regarding cavity barrier inspections:
- Are Cavity Barrier Inspections intrusive?
Cavity barrier inspections are non-intrusive - Will they leave visible marks on the building?
typically, Cavity barrier inspections do not leave any visible marks on the building - How long do inspections typically take?
The duration of inspections depends on the size and complexity of the building, but they are generally completed as efficiently as possible to minimise disruption - What are surveyors looking for during the inspection process?
Surveyors meticulously examine cavity barriers for any deficiencies, ensuring that they meet the required fire safety standards.
Frequency of Inspections
The frequency of cavity barrier inspections varies depending on several factors, including the type of building, its usage, and the prevailing fire safety regulations. However, as a general guideline, regular inspections should be conducted at least annually to maintain compliance and address any potential issues promptly.
Cavity barrier inspections are a vital aspect of fire safety management in buildings across the UK. By adhering to regulations and standards, conducting thorough inspections, and addressing any identified deficiencies, property owners and managers can enhance the fire resilience of their structures and safeguard occupants' lives and assets.
At Ventro Group, we emphasise the importance of proactive fire safety measures, including regular cavity barrier inspections, to mitigate the risk of fire incidents and ensure compliance with regulatory requirements. For professional guidance and assistance with cavity barrier inspections and other fire safety services, contact Ventro Group today.
Sign up for fire safety updates
You'll receive all the latest news and blogs straight to your inbox.